Frequently Asked Questions
Do I need to obtain an RMA (Return Materials Authorisation) before returning items for service or calibration?
Yes, you will need to request an RMA number by completing this form and returning to our Service team at service@tritech.co.uk prior to the return of equipment. Please ensure your RMA number is shown prominently on the documents/labels accompanying your shipment.
Where do I need to return equipment for repair or calibration?
If you are in the UK, please obtain an RMA number and return all equipment for service or repair to the following address*:
Tritech International Limited
Design, Manufacturing and Service
Oubas Hill
Next Ness Lane
Ulverston
Cumbria
England
LA12 7LB
United Kingdom
If you are not in the UK, please locate your nearest Tritech local representative here.
Do you have any advice for sending products from outside of the UK?
Yes, you can find some useful information here..
How do I find out about the status of my equipment that was returned for repair or calibration?
Please contact our Product Service Team by either emailing (service@tritech.co.uk) or telephone (+44 (0) 1224 744 111) (option 1). Please ensure that you state the Tritech serial number of the unit as this will aid us in finding your equipment quickly.
Where can I find the product retirement notices?
The retirement notices can be found in the Resources page. To go directly to them click on the link "Retirement Notices"
Where can I find the product technical notices?
The technical notices can be found in the Resources page. To go directly to them click on the link "Technical Notices"
Is the MicronGemini compatible with the Diver Mounted Display?
Yes! The MicronGemini has been integrated with the Diver Mounted Display.
How do I clean my Diver Mounted Display (DMD)?
We've created a video which you can watch here to explain how to clean your Diver Mounted Display (DMD).
How do I update my Diver Mounted Display (DMD) Subsea Computer?
We've created a video which you can watch here to explain how to update your DMD Subsea Computer.
What software should I use with the Gemini 720is?
Genesis which can be downloaded here.
My SCU reports a TMO COM AIF Error on Com Port 1 – should I be worried?
On new systems, Seanet Pro, the Tritech software that runs on the SCU, is looking at Com Port 1 for sensor information. If it doesn’t find any it reports the TMO error that you are seeing. If you do have a Tritech unit connected to that port which isn’t working, please contact our Customer Support Team (on +44 (0) 1224 744 111 (option 2), or support@tritech.co.uk).
If you do not have a Tritech unit connected to that port you can either ignore the error or disable the Com Port in the Seanet Pro software by doing the following:
- Go to the Utilities drop down menu and select Com Setup
- For the AIF device that has Com Port 1 selected, ensure that the Enable box is unchecked
- Close the Com Setup window
Product Repair and Service
If you are unable to find a solution here, please email the Product Service Team at: support@tritech.co.uk or call us on +44 (0) 1224 744 111 (option 1) where we would be delighted to assist you.
My device shows as UNKNOWN in Seanet Setup. What does this mean?
This is nearly always an issue with the RS232 ground which is usually missing. Check for continuity on the copper sections between each end of the cable.
On the small chance it is not, then it is a RS485 device connected to an RS232 port.
This document will help get the basics sorted out - Serial Port Connection and Setup rev 1
What is the difference between the Gemini 720ik and the Gemini 1200ik?
The Gemini 1200ik is a dual frequency version of the Gemini 720ik. The operating frequencies are 720kHz and 1200kHz for close inspection.
Why are the appendices in the PA Altimeter manual blank?
The PA range of Altimeter products available from Tritech come in a wide variety of connector, material and electrical wiring options. As these variations can, at times, be highly specific and individual to a single Altimeter, we utilise the Appendices to tailor the manual for individual customers at point of sale.
How can I get the pin out or material information for my Altimeter?
Please contact Tritech’s Customer Support Team (on +44 (0) 1224 744 111 (option 2), or support@tritech.co.uk) with your Altimeter’s full serial number (e.g. S02125.123456) and they will be able to forward you full details of your unit.
Where can I find the calibration frequency for Tritech products?
The calibration frequency guidance document can be found under the technical notices in the Resources page. To go directly to them click on the link "Technical Notices"
Alternatively, the document can be accessed here: Calibration Frequency Guidance
Can I get a copy of the Calibration Certificate for my Bathymetric system?
Please contact Tritech’s Customer Support Team (on +44 (0) 1224 744 111 (option 2), or support@tritech.co.uk) with the full serial number of your Bathymetric system (e.g. S03690.987654) and they will be able to forward you an electronic copy of the original, or last known, calibration – as performed by our in-house calibration facility.
Is there a development kit for the MicronNav system?
Currently there is not a Software Development Kit for the MicronNav System in either the Genesis or Seanet SDK.
How is it best to approach the Seaking SDK? Settings and getting started?
Having the hardware is the ideal place to start. Without this you have to rely 100% on the documentation.
Without the hardware you will have to copy the data as it is in the documentation and work from there.
With the hardware I would recommend running the head in Seanet Pro and snooping both the Tx and Rx line to see the data being sent between the sonar and the computer. This will allow to see the hex data and which fields are changed when you change the settings in Seanet. This will help you to make sense of the headers and nomenclature.
I see the Genesis start-up screen then it does not seem to open.
If you have changed your monitor configuration or moved the Genesis application offscreen, Genesis will open up and you will find it difficult to access.
To fix this, you you need to delete the Genesis folder within the Windows AppData folder. This can be found at the location below:
C:\Users\XXXXXXX\AppData\Roaming\Tritech
Where XXXXXXX is your local computer ID.
Which software download should I use?
If you have a computer running Windows, desktop or Laptop, then you should download the version "for PC/Laptop"
If you have a Hammerhead then you will need to use the "For Hammerhead" download. Note this is for a PC/Laptop too.
The SCU versions are ONLY for Tritech SCU units. These will not work on the Windows versions that run on every day Personal Computers or Laptops.
How does multibeam sonar work?
Tritech’s multibeam sonars, such as the Gemini 720is, all share the same principle of operation. A transmitter is used to convert electrical energy into sound energy in the water over a wide sector (transmit) and a separate receiver arranged as a linear array of multiple elements is used to convert sound energy from the same wide sector back to electrical energy (receive). With reference to Figure 5, the transmitter is curved over an arc of angle ‘A’ and with a height ‘H’ determine the horizontal and vertical acoustic beamwidth for a given frequency.
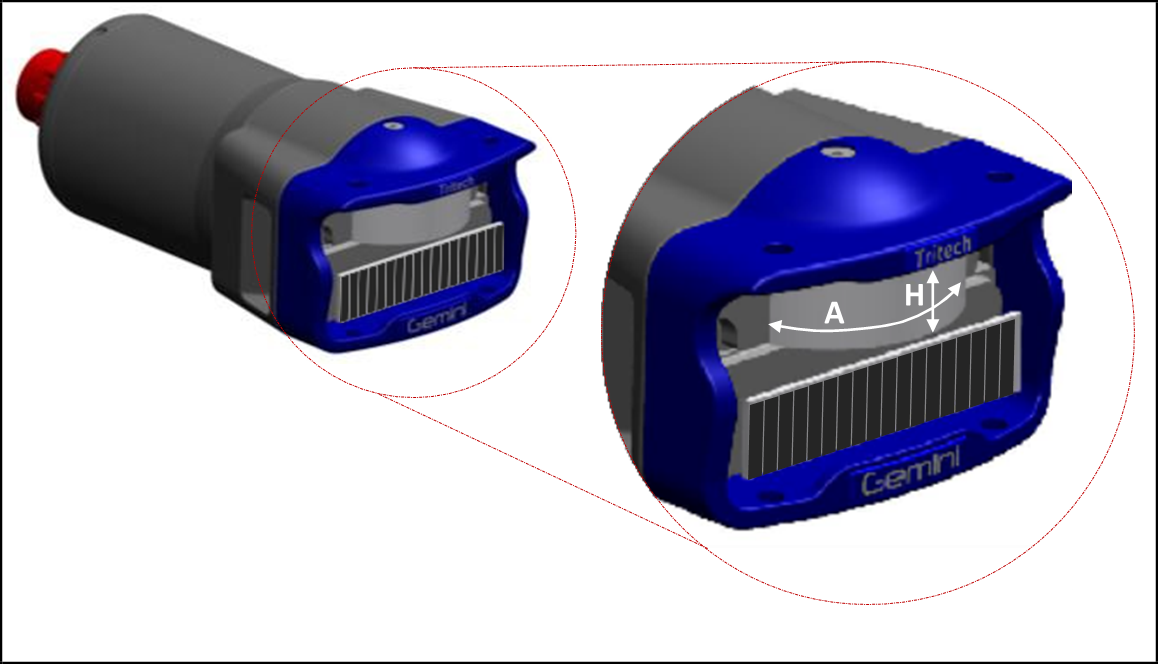
Figure 5 – Multibeam Sonar: Transmitter Parameters
The horizontal beamwidth is significantly larger than the vertical beamwidth, as illustrated in Figure 6. During transmission electrical energy is converted into a wide fan of sound energy in the water in a direction normal to the front face of the centre of the transmitter.

Figure 6 – Multibeam Sonar: Transmitter Ensonification
With reference to Figure 7, the receiver is a linear array of multiple elements. Each element has a width ‘W’ and height ‘H’ that determines the horizontal and vertical acoustic beamwidth, for a given frequency, of that element. The vertical beamwidth of the receiver typically matches the vertical beamwidth of the transmitter to maximise overall sensitivity. All the elements are identical and when positioned side by side the overall length of the array ‘L’ determines the horizontal acoustic beamwidth for a given frequency of the receiver as a whole. To obtain a smaller horizontal acoustic beamwidth the array must increase in length.

Figure 7 – Multibeam Sonar: Receiver Parameters
With reference to Figure 8, the horizontal beamwidth of each element is significantly larger than the horizontal beamwidth of the array.

Figure 8 – Multibeam Sonar: Receiver Beamwidth
By transmitting sound energy over a wide fan on reception any sound energy emanating from targets within the wide fan will be converted to electrical energy by each element in the linear array.
Sound energy, an echo of what was transmitted, from a target normal to the receiver, in the far field (sufficiently far away) will be received by every element in the array at practically the same time. Much in the same way a mechanically scanning sonar works, by timing how long it takes for sound energy to be received and knowing the speed of sound in water the spatial distance of a return from a target can be calculated. The strength of the return from a target can also be calculated by observing the magnitude of the sound energy received, compensating for any losses as the sound travels through the water. The beam normal to the receiver is formed by the accumulation of the sound energy across all elements in the array. The beamwidth of this beam is determined by the length ‘L’ of the array for a given frequency, as illustrated in Figure 9.

Figure 9 – Multibeam Sonar: Receiving (Far Field)
All other beams, not normal to the receiver, are formed individually by the accumulation of the sound energy across all elements in the array delayed depending on the angle ‘A’ of the beam. The delay applied to each element is determined by the extra distance ‘ΔD’ travelled to that element, as illustrated in Figure 10. Knowing the speed of sound in water the delay can be expressed in time rather than distance. Thus, Tritech’s imaging multibeam sonars provide true time delay beamforming (TDB) and built in speed of sound sensors accurately, and continuously, ensure that the delays applied generate the most representative image.

Figure 10 – Multibeam Sonar: Receiving (Far Field) Angle
Sound energy, an echo of what was transmitted, from a target normal to the receiver, in the near field (sufficiently close), will be received by every element in the array at different times. This is because sound energy emanating from a single point travels in an arc of ever increasing diameter. Indeed an echo from a target in the far field also generates an arc of sound energy. However, once the distance is great the portion of the arc that ensonifies the receiver can be considered planar and therefore treated as a straight line.
Forming beams from an arc of sound energy in the near field is the same process as the far field. However, the delay applied to each element is determined by the curvature of the arc, as illustrated in Figure 11, as well as the angle of the beam.

Figure 11 – Multibeam Sonar: Receiving (Near Field)
The curvature of the arc changes with distance from the receiver and angle. By compensating for the curvature of the sound energy Tritech’s multibeam sonars with TDB provide near field focusing allowing image formation down to 0.2m range.
To build up an image over a sector, beams are formed simultaneously at multiple angles, by applying a different set of delays to the elements and accumulating. The acoustic beamwidth of the array, determined by its apparent length of the array, is dominant. Therefore, whilst it is possible to form numerous beams within one steered acoustic beamwidth forming more beams doesn’t improve the image. Thus, a complete image can be generated after only one acoustic path transit time, as illustrated in Figure 12, resulting in a very high update rate, several orders of magnitude faster than a traditional mechanically scanning sonar. Thus mitigating the problem with artefacts in the image due to sonar or target movement.

Tritech’s multibeam sonars provide high quality sonar imagery at video framerates. This maximising the effectiveness of subsea operations and allows completion of tasks sooner, more safely and with more accuracy.
How does a USBL System Work?
How does a USBL system work?
The Tritech MicronNav 200 is a USBL positioning system. USBL stands for Ultra-Short Baseline, but knowing that alone doesn’t offer much insight into how the system works. This short article aims to explain a little more about the system and how to get the best out of it.
Radio frequency signals are heavily attenuated by water, and so radio-based positioning systems like GPS cannot be used underwater. The solution is to use acoustics. Sound, particularly at low frequencies (such as the 20 kHz to 28 kHz band where the MicronNav 200 system operates) can travel large distances through water.
What is an acoustic positioning system?
An acoustic positioning system comprises two main elements: the USBL head (sometimes called the dunker) near the surface, and one or more remote modems, also called transponders or beacons. The USBL head may be mounted to a vessel or simply deployed on a pole from somewhere like a jetty. The modem(s) may be mounted to ROVs, divers, or any other object whose position is to be tracked.
The system works by the USBL head transmitting an acoustic message to interrogate one of the modems; this message includes an address, so that only one modem will reply. When the addressed modem receives this message, it will respond with an acoustic signal, which is in turn received by the USBL head. The system may then move on to interrogating other modems, one at a time.
How does the system measure range?
The time delay between the USBL head transmitting and receiving a response is used to calculate the distance (slant range) between the USBL head and the modem. Sound travels in water at around 1500 m/s (it varies due to factors such as salinity, temperature and pressure), and so with knowledge of an accurate speed of sound, an accurate slant range can be calculated.
How does the system measure angles?
The slant range alone is only a one-dimensional (1D) position fix. To calculate a three-dimensional (3D) position, two additional pieces of information are needed: the horizontal and vertical angles between USBL head and the modem. A USBL system obtains this additional information by using an array of receiving hydrophones inside the USBL head; in the case of the MicronNav 200, four receiving hydrophones are used. The system measures the phase difference between the signals arriving at each of the hydrophones, and uses this to calculate the angle of arrival of the acoustic signal from the modem.
The distance between the receiving hydrophones is known as the Baseline, and in the case of a compact system like the MicronNav 200, the distance is commonly referred to as Ultra-Short. Alternative (e.g. Long Baseline) systems may spread receiving hydrophones along the length of a ship, or at multiple fixed locations, trading cost / practicality / complexity for improved angular accuracy.
How does geo-referencing work?
Having measured the slant range and horizontal / vertical angles, the system can now calculate a 3D position for the modem. At this point however, that calculated position is relative to the attitude, heading and position of the USBL head. To account for the attitude and heading of the USBL head, the MicronNav 200 USBL head conveniently includes an integrated magnetic compass and pitch & roll sensor. To account for the global position of the USBL head, the system accepts an external input from a GPS or similar positioning system.
With all of this in place, a USBL system can now calculate and display geo-referenced positions of multiple tracked modems on charts.
What practical difficulties may be encountered?
Like all acoustic systems, USBL positioning systems are affected by the underwater acoustic environment. Noise from wave motion, ships engines, depth sounders etc. can interfere with operation of the system. The MicronNav 200 uses spread spectrum (chirp) acoustic pulses for robust operation in noisy environments. The chirp pulses have a unique acoustic signature which can be isolated from background noise.
Multipath reflections can also present difficulties for USBL systems, since the reflected acoustic signal is a time-delayed copy of the direct-path signal. Sound reflects most strongly when it meets an object with a significantly different density to water: rock, steel and air (bubbles or the water surface) are good examples of this.
Where the reflecting surface is irregular, the reflections tend to be broken up and interfere destructively with each other so as not to present a problem. Where the reflecting surface is large and flat (such as a ship’s hull, a rock wall or the water surface on a calm day), then it acts as an acoustic mirror, presenting a near-perfect copy of the original signal. Correct mounting of both the USBL head and the modem is critical to reliable system performance. They must both be placed at least 1m away from large flat reflecting surfaces.
What additional features might be useful?
A USBL system may also include additional features such as:
- Modems with integral rechargeable batteries, for convenient deployment with divers, but also to act as a backup lost ROV locator in case the ROV tether is severed.
- Options to trigger the modem electrically rather than acoustically; this is known as responder mode (in contrast to the more usual transponder mode). This halves the acoustic round-trip time and allows a higher position update rate. It may also help when interleaving USBL signalling with other acoustic systems in use.
- Data transfer features, where arbitrary user-supplied data is added to the acoustic messages exchanged between the USBL head and modem. This may allow short text messages to be exchanged with a diver, or for a remote seabed data logger to be interrogated.